[ad_1]
Q&A with Lucid’s Battery Cell Technical Specialist Maithri Venkat.
On the subject of battery cells for EVs, one measurement undoubtedly doesn’t match all. The properties of a selected cell act as constraining components for each facet of a car’s design—and never just for car efficiency parameters comparable to vary and energy, however for the event of producing processes as nicely.
Lucid Motors has a crew of battery specialists that collaborates intently with cell suppliers to judge and check battery cells at each step from car design via mass manufacturing. Charged spoke with Lucid Battery Cell Technical Specialist Maithri Venkat about how cell analysis works, and the way OEMs and cell suppliers can work collectively to enhance the method.
Charged: Might you inform us about your self and your journey to your current position at Lucid Motors?
Maithri Venkat: I’ve been working in lithium-ion cell growth for automotive purposes for the previous eight years. In my present position as a Technical Specialist at Lucid, I lead next-generation cell choice, qualification and key provider partnerships for the Gravity SUV. I’ve labored on a number of points of battery growth, from cell materials analysis to design tradeoff assessments to efficiency optimization and new product introduction.
Beforehand, I labored at XALT Power, the place I benchmarked cell designs and sub-components for high-energy cells for transportation and marine necessities. I’ve additionally collaborated with top-tier OEMs and nationwide labs for 12 V Li-ion begin/cease battery growth.
For efficiency purposes, an organization must know learn how to push the restrict. For economic system choices, the cells are the most important price driver within the car.
Charged: Are you able to elaborate on why battery cell growth is so vital for electrical autos?
Maithri Venkat: As automakers decide to electrification, the market necessities have gotten extra various for various kinds of EV merchandise—longer vary, quicker charging, sports activities car-level efficiency numbers and lengthy life. The battery cell impacts all of those.
How one designs, tunes and manufactures the battery cells additionally impacts their effectiveness, efficiency and price. For efficiency purposes, an organization must know learn how to push the restrict. For economic system choices, the cells are the most important price driver within the car.
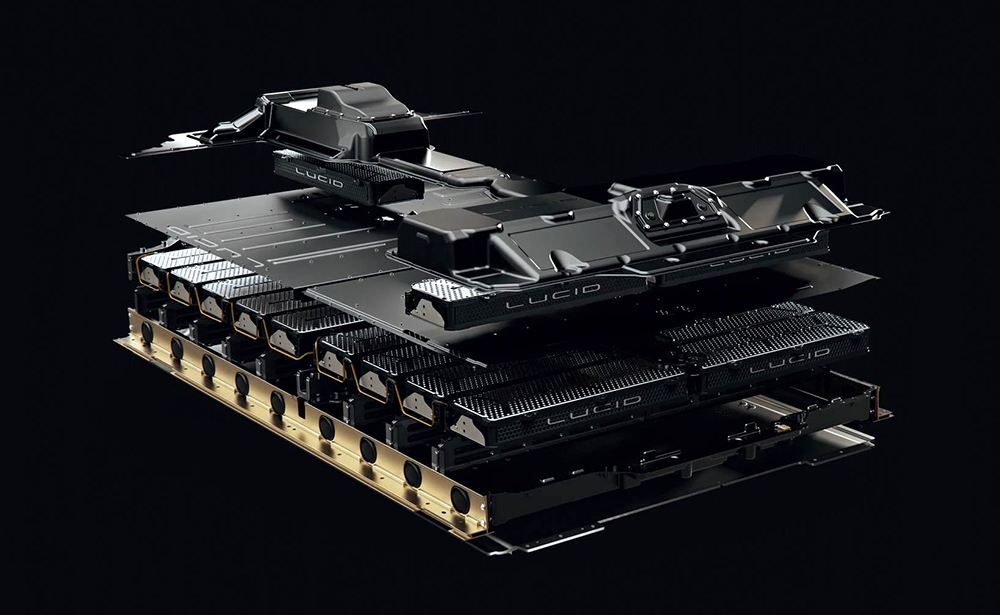
Battery cell growth is essential at each step of the event of a car, however particularly firstly conceptual design section, the place the vehicle-level product definitions are translated into cell-level technical specs. Technical assessments and business necessities are evaluated by EV producers throughout cell choice and qualification. As soon as the cell design is finalized, it’s fine-tuned additional for vitality effectivity, quick cost functionality, energy functionality and lifelong necessities, previous to deployment in packs and autos. This early stage of cell growth paves the way in which for best-in-class technological developments.
As soon as the cell design is finalized, it’s fine-tuned additional for vitality effectivity, quick cost functionality, energy functionality and lifelong necessities, previous to deployment in packs and autos.
Charged: Are you able to stroll us via the preliminary phases of the cell qualification course of? What do we have to take into account even earlier than going into cell choice?
Maithri Venkat: Cell growth for automotive purposes must occur years upfront. This ensures that we now have sufficient time to iterate via cell design modifications. Normally, cell growth begins with the creation of vehicle-level efficiency targets.
For instance, a car’s meant usable vary is a key metric within the qualification course of. Goal vary necessities are outlined primarily based on an array of analysis, together with advertising surveys and shopper suggestions. With these established, we are able to apply technical constraints comparable to car and powertrain effectivity, pack sizing and car weight class, to remodel vary into usable vitality per cell.
Previous to defining battery pack constraints, we have to analyze and steadiness efficiency, sturdiness and price. This requires in-depth collaboration amongst cell engineering, methods, car integration, effectivity, software program and advertising groups.
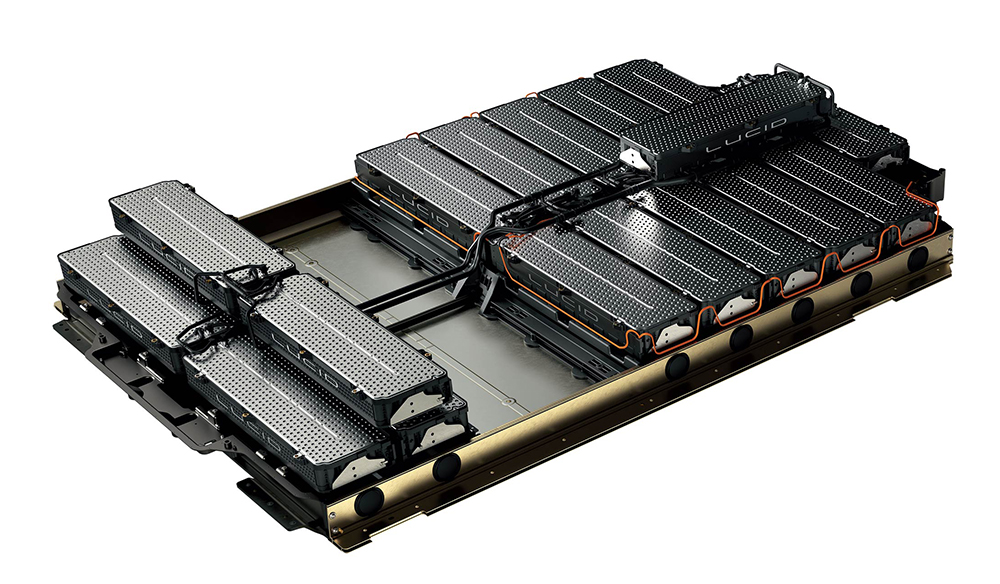
Following car definitions and alignment on cell efficiency aims, specification sheets are despatched over to cell suppliers. This creates an iterative suggestions loop between OEM and cell provider, and triggers hole evaluation between necessities and expertise readiness.
Figuring out these efficiency gaps and quantitatively understanding the constraints of particular cell chemistries helps with future cell growth. As an example, for high-energy cell design, material-level modifications comparable to silicon for anodes, high-nickel cathodes, or solid-state chemistries might be thought-about. This is able to allow technological developments and outline clear actionable aims to bridge the variations between current-generation and next-generation applied sciences.
Charged: You talked about the necessity to translate vehicle-level necessities into cell-level targets. How can we accomplish that?
Maithri Venkat: As soon as the car conceptual design has been finalized, necessities trickle right down to pack and module ranges earlier than getting right down to cell-level definitions.
Each high-level goal could be tied to a person parameter of the battery cell. For instance, pack measurement, effectivity and vary could be outlined as vitality necessities for the cell. 20-80% SoC (state of cost) charging occasions could be translated to quick cost functionality of the cell. Product guarantee necessities [can be translated to] lifetime efficiency of the cell, and so forth. Kind issue choice could be depending on pack sizing methods, thermal administration methods for cooling, ease of manufacturability, and even ease of restore.
Cell peak or steady energy targets are associated to the 0-60 mph car efficiency necessities and towing capability. Detailed energy functionality evaluation is useful to offer the required efficiency if you need to—for instance—tow your jet ski to Lake Tahoe. Or, on the way in which residence, roll down a hill and regeneratively brake at freezing ambient temperatures for over an hour.
Charged: What are the steps an organization takes to qualify a brand new cell provider?
Maithri Venkat: We consider cell suppliers for a number of prime priorities, together with security, high quality, price, efficiency, volumes, expertise roadmap and expertise capabilities.
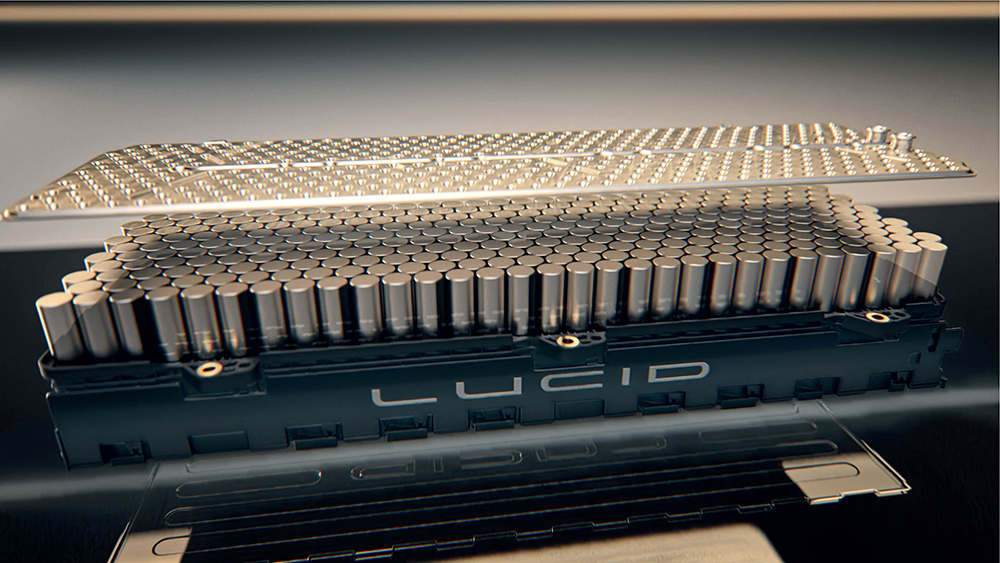
For instance, in terms of cell high quality inspection, manufacturing batch lot-to-lot variation have to be throughout the outlined engineering specs, and course of variations must be inside Six Sigma management limits. Within the preliminary phases, routine beauty and electrochemical inspections should be performed on obtainable samples. Cell dimensional properties and look of dents, rust or scratches must be totally assessed to grasp manufacturing course of functionality. For electrochemical inspection, it might even be advantageous to conduct common testing for efficiency traits like vitality and resistance. If cell-to-cell vitality variations exceed sure threshold values, there are dangers when it comes to battery pack imbalances.
One other facet to contemplate is the provider timeline. Auto producers want to make sure that their growth timeline aligns with the cell producer’s milestones for idea, design and course of validation phases. Cell mass manufacturing must be nicely upfront of the product introduction timeline.
Charged: As soon as a cell design is finalized, what are the subsequent steps to be thought-about? What forms of assessments are applicable for every developmental section?
Maithri Venkat: Following cell design finalization, a number of workstreams occur in parallel as a part of the product growth cycle. I’m at the moment main and facilitating these efforts for Lucid’s Gravity SUV platform. These embody quick cost, sturdiness, course of functionality, cell parameterization for software program controls, and testing for state of well being/thermal modeling. Listed below are some examples of that course of circulation at Lucid:
Parameter measurements: As soon as consultant cells can be found from the producer, an in depth suite of cell testing and information processing is kicked off for Equal Circuit Modeling (ECM) growth. The cell parameter datasets obtained from testing are important for correct state of cost (SoC) and state of well being (SoH) estimation.
Utilizing precise cell testing information, we are able to get insights into establishing management limits, and hint how the gaussian vitality distributions would scale up at pack degree when cells are distributed in collection and parallel connections.
Variability research: From the method functionality facet, it’s important to trace cell-to-cell variability via design validation, course of validation and closing mass manufacturing phases. This helps car methods modeling, integration and product groups gauge the estimated vary and efficiency for the ultimate product. It’s additionally vital to characterize nominal capability and vitality distributions after analyzing consultant drive profiles with discharge/regeneration pulses included inside testing intervals. Utilizing precise cell testing information, we are able to get insights into establishing management limits, and hint how the gaussian vitality distributions would scale up at pack degree when cells are distributed in collection and parallel connections.
Optimization: Miles charged per minute defines quick cost capabilities. Complete testing is finished at cell, module and pack ranges to grasp the failure modes and lithium plating thresholds over the cell lifetime. This facilitates the number of quick cost profiles and helps push the efficiency boundaries.
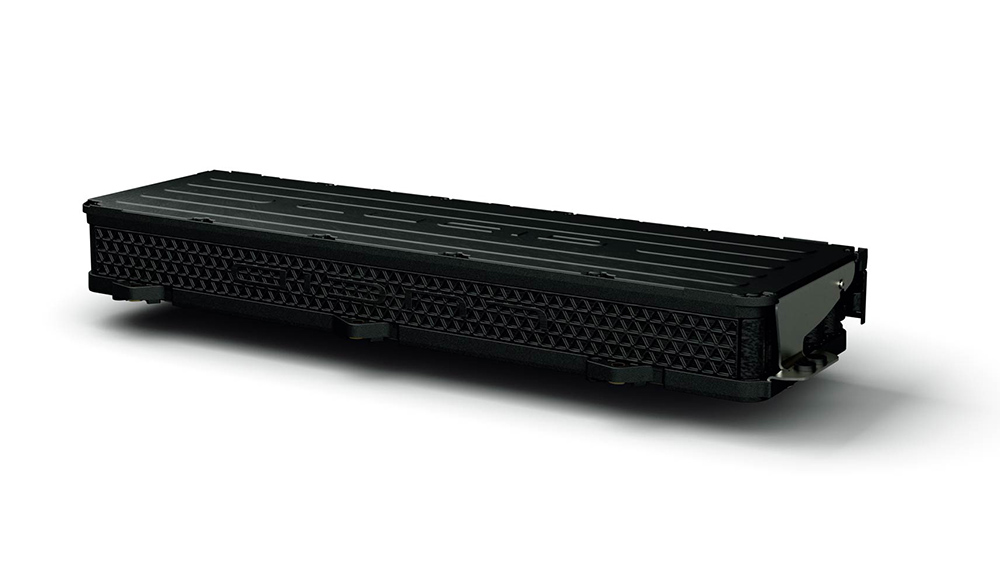
Modeling: State of well being (SoH) for lithium-ion batteries must be predicted precisely for software program controls and for prolonging cell usable lifetime. Physics-based cyclic and calendar growing older capability decay fashions are developed to seize lack of optimistic/destructive electrode materials and lithium stock over battery utilization.
Charged: What are some frequent misconceptions about defining cell specs for automotive utilization situations?
Maithri Venkat: Cell engineering specification sheets are extraordinarily conservative in sure instances. For instance, laboratory cell biking with 1C cost and 1C discharge might set off surprising degradation modes like lithium plating and gasoline era. Within the case of the Lucid Air Dream Vary version, the car’s vary is 520 miles at prime of cost, and 1C discharge would imply depleting 520 miles in a single hour. That is an not possible situation in the true world, even when we assume the bottom efficiencies throughout discharge. Cells are way more succesful after we conduct experiments underneath the vary of circumstances accessible to a buyer. It’s due to this fact vital to contemplate that testing underneath the fitting circumstances will help entry extra consultant limits of efficiency boundaries. As an analogy, Olympic groups don’t decide their marathon runners primarily based on their efficiency in a 100-meter sprint!
Moreover, sure provider specification sheets are primarily based on shopper electronics, for which vitality estimations are calculated with extraordinarily low constant-voltage cutoffs on the finish of charging periods, or cells are cycled repeatedly between zero and 100% state of cost. Customers of EVs hardly ever cost to 100% after which drive right down to zero. In consequence, it doesn’t all the time make sense to carry out testing and specification setting with such utilization patterns.
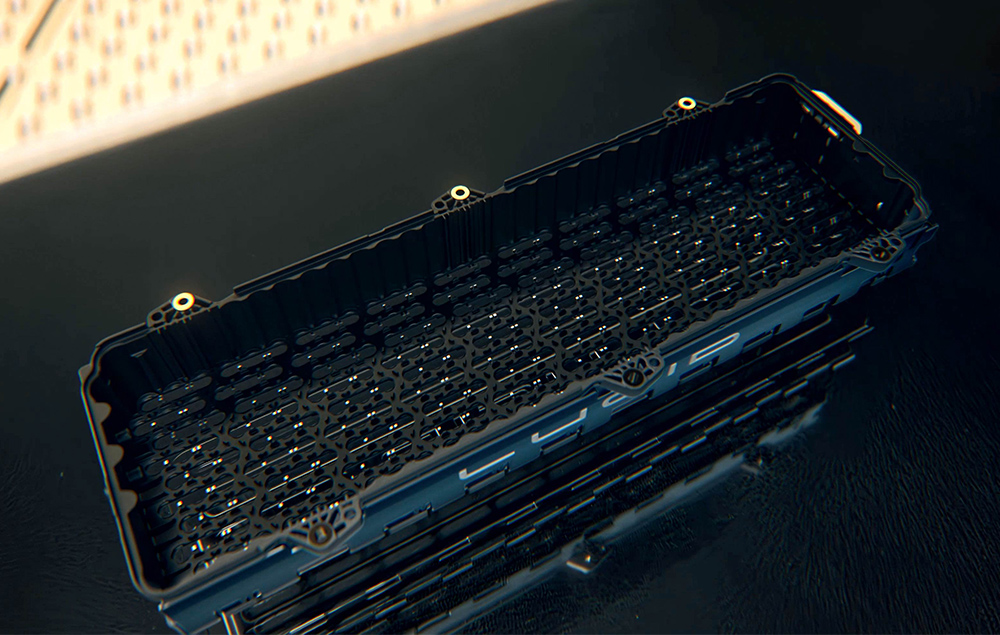
Charged: How can automotive firms assist cell suppliers develop specs?
Maithri Venkat: We must always be sure that provider specification sheets match automotive use instances. I acknowledge that it’s difficult to specify an actual automotive use case. Nevertheless, it might nonetheless be invaluable to rewrite the specs to evolve extra intently to what clients may expertise.
At Lucid, battery information scientists use fleet telemetry information to grasp real looking utilization profiles. Quick cost efficiency boundaries are evaluated primarily based on the popular charger sort, temperature regimes and state of cost (SoC) for session starting and finish. Automotive firms can educate cell suppliers quite a bit which will return into their growth processes and assist them make a greater product.
Subsequently, it might be helpful to have steady communication between cell producers and OEMs for incorporating shopper utilization profiles in engineering specs.
Lastly, it might be helpful for automotive firms to drive specs growth. Finally, this serves one of the best pursuits of each cell suppliers and OEMs.
Charged: You talked about real looking profiles earlier. How can we incorporate real-world growing older into laboratory testing? Is there a technique to strike a steadiness between utilizing aggressive growing older vs real looking growing older profiles for cell evaluations?
Maithri Venkat: It’s of paramount significance to grasp the tradeoffs related to utilizing aggressive vs real looking growing older profiles previous to figuring out the design of experiments for laboratory cell assessments. Testing strategies involving slower cost/discharge, lowered depth of discharge and common temperatures could be perfect for replicating typical EV utilization. Beneath these circumstances, lithium-ion batteries would expertise the degradation mechanisms comparable to strong electrolyte interphase (SEI) development which are noticed in real-world driving. Nevertheless, this might additionally indicate for much longer check timelines to acquire capability loss and resistance development information.
Then again, utilizing accelerated growing older might lead to lithium plating on the anode as a consequence of diffusion limitations or gasoline era from electrolyte solvent discount reactions. Whereas the testing time is lowered, the failure modes aren’t consultant and even achievable for these nook instances.
Ideally, one wants to decide on intermediate cost/discharge charges with relaxation steps included between cycles for efficient efficiency scale-up.
Charged: What are the cell pattern portions needed for every developmental section?
Maithri Venkat: Cell pattern measurement required will improve via the developmental phases. For provider analysis and cell design screening, it might be ample to begin with a whole lot of early R&D pattern cells. Nevertheless, as soon as the design is confirmed, efficiency optimization and sturdiness testing would require 1000’s of cell samples. After this, we get into module and pack testing. The cell amount required for that is 10 occasions extra in comparison with the earlier section. Subsequently, the ultimate car testing section would require over 100 occasions extra from the mass manufacturing line in comparison with preliminary R&D evaluations. It is very important do not forget that bigger portions for cell allocations should be obtainable far upfront of the beginning of auto manufacturing.
Charged: Why are consultant battery packs required for car testing months upfront of the beginning of manufacturing?
Maithri Venkat: That is associated to the kind of car validation and regulatory assessments being performed. Having an early begin to validation helps offset longer lead occasions related to testing and information procurement. Examples embody car fleet deployment, scorching/chilly climate local weather testing, homologation and SoC/SoH software program algorithm validation. Electrical autos have to undergo mileage accumulation and standardized sturdiness testing to make sure constant long-term efficiency, reliability and guarantee assurance.
Charged: Finally, the objective is to get cells into automobiles. What could be a few of the key duties that we have to observe whereas transferring in the direction of manufacturing scale-up throughout EV manufacturing?
Maithri Venkat: Even after finishing efficiency optimization and reliability assessments, we nonetheless should be aware of recent product introduction within the manufacturing unit. As we transfer in the direction of manufacturing ramp-up, we have to take into account cell integration into modules and packs on the manufacturing stage. Every cell sort must have a definite manufacturing half quantity, gear settings, and even information dealing with. Even mundane modifications like barcode placement on a cell field can dramatically affect yield if course of controls aren’t totally optimized.
One other instance is the implementation of totally automated in-line inspection strategies for checking key cell traits. These high-speed measurements, together with mid-process and end-of-line measurements, assist us be sure that the processes concerned in constructing modules and packs haven’t impacted the integrity or efficiency of our cells.
Charged: What concerning the general timing? How a lot time can we sometimes have to qualify a cell for automotive utilization?
Maithri Venkat: Cell growth for automotive purposes occurs years upfront. Since each cell has distinctive traits, it’s important to conduct detailed testing all through the qualification phases to probe into cell degradation mechanisms and consider efficiency thresholds.
We would want to judge the event timeline on a person foundation. The time required could be depending on necessities, expertise readiness, cell chemistry, manufacturing feasibility, and the meant EV utility and market. Talking typically, it’s a few years.
It’s also doable that even a secular course of change from a cell producer might have unintended but extreme impacts downstream for an automotive maker. Subsequently, each single change to a cell must be scrutinized.
Let’s additionally take into account a situation during which the cell chemistry is frozen, and there’s a change with respect to a minor course of throughout manufacturing. Whereas this may create a major enchancment in yield, the crew nonetheless wants to judge if it has an affect on efficiency or security. For this instance, it’s doable that a complete re-qualification of the cell will not be required, and the change could be shortly accredited. Nevertheless, it’s also doable that even a secular course of change from a cell producer might have unintended but extreme impacts downstream for an automotive maker. Subsequently, each single change to a cell must be scrutinized. I need to spotlight that each cell is exclusive. Qualification methods and developmental timelines should be evaluated on a case-by-case foundation. Battery cells could be one of the essential path objects in your EV growth.
This text first appeared in Concern 66: October-December 2023 – Subscribe now.
[ad_2]