[ad_1]
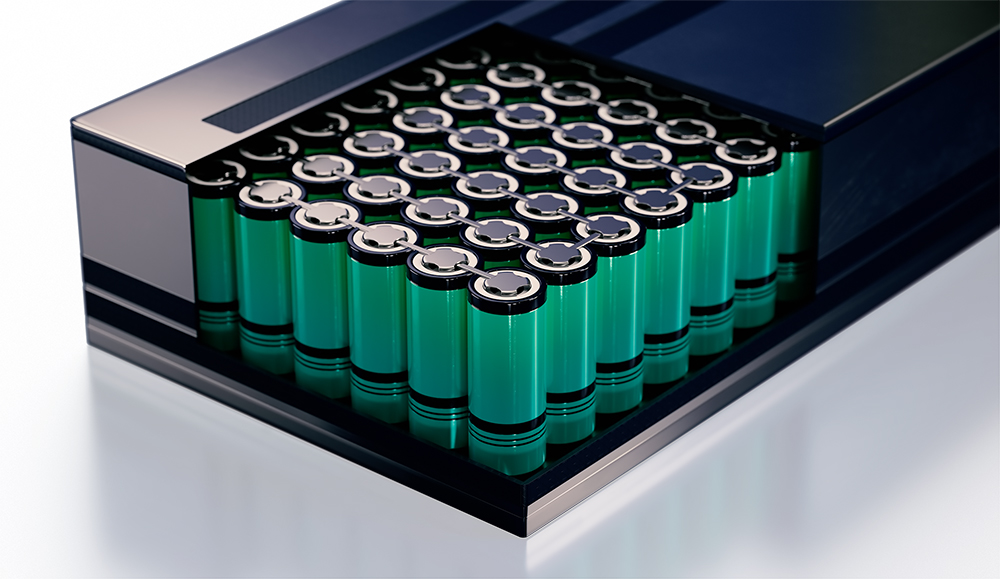
Because the vitality transition and electrification of mobility drive the explosive demand for batteries, Christophe Mazeaud, director of Battery Trade Answer, Siemens Digital Industries Software program, discusses the important thing position {that a} holistic high quality program performs in scaling and stabilizing battery manufacturing.
What we’re seeing throughout the battery manufacturing panorama is a rare drive to satisfy unprecedented demand, and this atmosphere makes digital options important to reaching high quality, price, quantity and supply targets. High quality administration is on the coronary heart of those efforts. Solely a digital manufacturing answer that integrates a high quality tradition all through the design and manufacturing cycle permits cell, module and pack producers to effectively scale and stabilize manufacturing on this extremely difficult market.
Market tendencies and manufacturing challenges
The quickly growing demand we’re seeing for batteries is propelled largely by climate-driven market forces, together with accelerated manufacturing of electrical automobiles and vitality storage options, in addition to numerous monetary incentives from governments the world over. These governments hope to encourage native improvement of gigafactories (vegetation with annual manufacturing capability measured in gigawatt-hours) and to reap the financial windfall that might observe.
In response, producers are getting into the battery market in massive numbers, resulting in greenfield manufacturing unit improvement in practically each world area and refurbishing factories by present battery makers and automotive OEMs. These developments lead each to cost stress and to the necessity for steady product innovation and course of enchancment. Underneath such situations, it’s difficult for brand new and skilled producers alike to supply high-quality batteries profitably and at scale.
Three main traits of right now’s battery business contribute to this problem. First is the novelty of the business. The microstructure and chemical composition of battery supplies have a substantial influence on high quality and battery efficiency, and the interdependencies of supplies and processes alongside the worth chain usually are not but properly understood. Moreover, comprehending the interdependencies is a shifting goal, with fast-paced product and course of improvements continually underway as battery manufacturing matures. Technological newness makes it tough for each startups and incumbent corporations to set management parameters within the battery manufacturing course of.
The second difficult attribute of the business is the necessity for scalability. A battery manufacturing ecosystem, whether or not newly constructed or an present manufacturing unit, should be able to scaling quickly with out undermining battery high quality. With the exponential development in battery demand, all producers should rapidly ramp up manufacturing of every line, usually whereas constructing a number of traces and factories in parallel. This problem is compounded for startups who’re additionally rising their group on the similar time.
Third, compliance with stringent and rapidly evolving laws requires a excessive degree of traceability by three distinct sorts of producing: batch, steady and discrete processes. On this regard, greenfield corporations have a bonus over incumbents. They’ll flip this problem into a possibility by organising the proper info know-how/operational know-how (IT/OT) panorama, proper from the start. Traceability can then be supported by seamless connections throughout digital platforms.
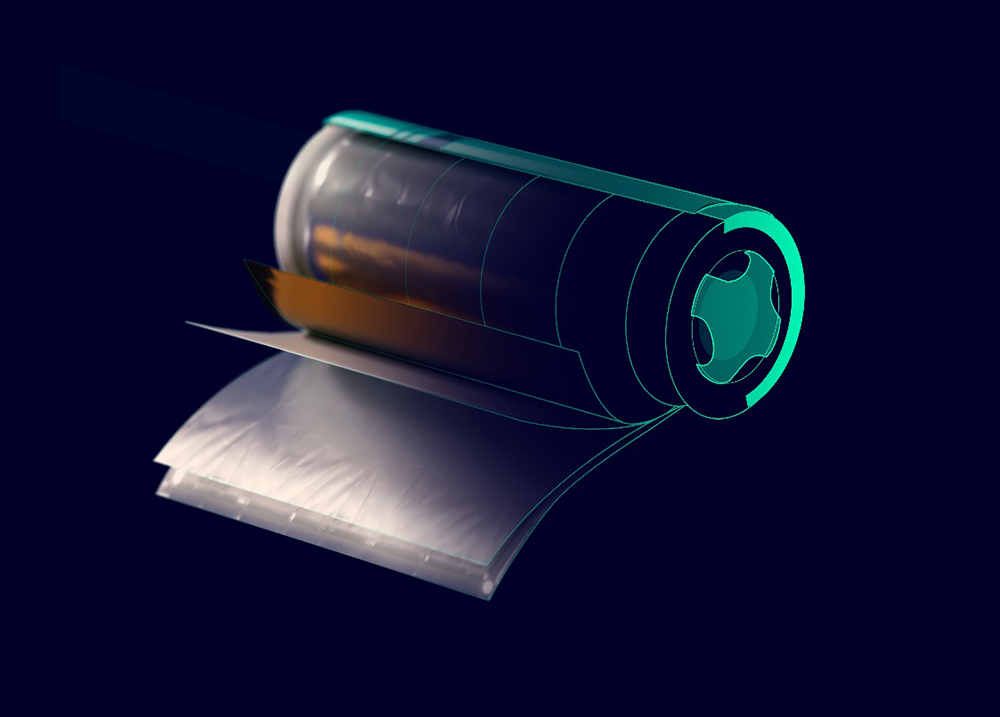
Constructing higher batteries sooner by leveraging progressive and superior digital options from battery design to battery manufacturing
Siemens Digital Industries Software program is collaborating with battery producers as they develop progressive manufacturing options to handle these challenges. By these collaborations, now we have realized the significance of digital manufacturing options for undertaking high-volume, high-quality battery manufacturing. If corporations are to manage and doc end-to-end high quality whereas additionally managing the complexity, innovation, and speedy scale that characterize right now’s battery manufacturing ecosystem, they have to determine the best way to speed up battery manufacturing by the entire product lifecycle and implement a wise manufacturing technique.
Delivering high-quality batteries requires you to handle totally different processes throughout the entire product lifecycle, from new product improvement to mass manufacturing. It’s important to design with a high quality mindset to speed up battery manufacturing. High quality engineers can leverage engineering information, equivalent to 2D or 3D fashions, to amass related info or carry out tolerance evaluations, and the venture high quality will be monitored and permitted in respective milestones. Dangers will be recognized, assessed, and mitigated within the digital product and course of constructions, and residual dangers will be managed by a management plan.
By “good manufacturing” we imply a digital technique that encompasses your complete manufacturing course of, from battery design and manufacturing unit ground optimization to streamlined orchestration of producing operations, to quick, correct sampling and testing. Sensible manufacturing absolutely integrates all digital methods to drive high quality and effectivity all through the battery manufacturing course of. To handle the quick tempo of battery innovation, a totally built-in digital method helps seize information gained as every new materials or course of is introduced into manufacturing. Manufacturing insights developed from this captured information can be utilized to enhance the subsequent product run and reused on the subsequent battery technology.
We’ve developed the Siemens Accelerated Battery Improvement and Sensible Battery Manufacturing options purposefully to assist battery corporations obtain manufacturing effectivity, readiness and excellence. That is achieved by built-in and standardized machines, processes and methods; digital multidisciplinary planning and simulation; and related, automated and constantly monitored traces.
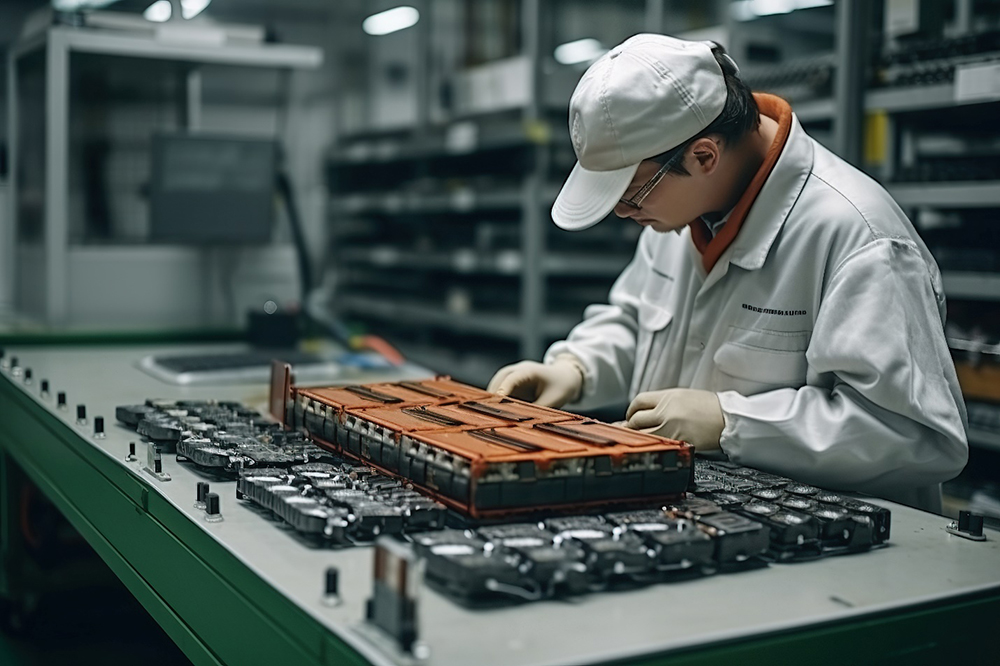
Reaching high quality excellence with a closed-loop high quality administration answer
In a digitalized ecosystem for the battery business, the standard tradition must be on the coronary heart. Siemens options orchestrate persistently processes all through the three main phases of battery improvement and manufacturing: (1) design and planning, (2) execution and management, and (3) steady enchancment.
Design for high quality and high quality planning—From the very begin of product improvement, battery designers should apply high quality tips and requirements from the automotive or different end-user markets. Shifting left, designers and engineers should type out issues within the digital realm relatively than discovering them on the manufacturing ground. With Siemens closed-loop high quality administration options, product, manufacturing and high quality engineers work concurrently in the identical digital atmosphere, leveraging digital fashions from one another’s efforts. For instance, design failure mode and results evaluation (FMEA) are constructed from the engineering invoice of supplies (eBOM). Product manufacturing info (PMI) contains 3D fashions, which function the place to begin for high quality management plans. Many different collaborative duties profit from the absolutely built-in digital answer.
A closed-loop high quality administration answer routinely maintains the traceability of adjustments, evolutions, and engineering selections, which is of nice profit to your complete battery engineering crew. Utilizing this answer, the crew can preserve the standard deliverable up-to-date and in sync with the necessities and engineering adjustments with considerably much less effort.
High quality execution and management— As a part of the depicted complete stream, two different methods inside the good manufacturing answer for batteries execute the just about outlined management plans digitally. These are the manufacturing execution system (MES) and the laboratory info administration system (LIMS). This holistic digital method enforces preventive high quality practices, avoiding human errors and getting the manufacturing line rapidly to a steady high quality degree.
For the battery manufacturing unit to achieve the subsequent degree of high quality and carry out predictive high quality management, information analytics capabilities inside the good manufacturing answer mix course of parameters, picture processing, product efficiency controls and environmental context, and leverages machine studying algorithms. In the end, the objective is to achieve the prescriptive high quality degree. Securing product high quality at this degree entails injecting information analytics into simulation fashions deployed on the edge to calculate and apply corrective actions on-the-fly.
Steady enchancment – In fact, defects or nonconformances (NCs) can’t be utterly prevented with robust planning or eradicated with fixed manufacturing course of monitoring. As an alternative, a wise manufacturing answer effectively manages nonconformances and permits quick response in addition to steady studying. Nonconformances are captured digitally and handled instantly on the shopfloor degree, whether or not they’re detected by incoming items inspection, in-line inspections or offline laboratory high quality management testing.
When required, sure high quality points are escalated to the engineering area to set off a correct root trigger evaluation. Inside Siemens digital threads, the problem-solving course of happens in the identical collaborative platform as product design, manufacturing planning and high quality engineering. Full integration permits centralized administration of points and actions, in addition to an intuitive identification of the required enhancements, in any area on the enterprise degree.
Not solely high quality points are handled rapidly, however actions are additionally taken instantly to forestall recurrence. Classes discovered are captured for the good thing about all departments and factories. The result’s really steady high quality enchancment.
Advantages inside the battery manufacturing plant and past
Effectively scaling and stabilizing the manufacturing of battery cells, modules and packs is the objective and first advantage of Accelerated Battery Improvement and Sensible Manufacturing options with a closed-loop high quality method.
Different direct advantages for the battery maker embrace:
- Decrease prices of poor high quality due to steady enchancment all through the entire product lifecycle
- Quicker time to market and scale-up due to cross-domain collaboration in a quality-driven product improvement
- Begin compliant and keep compliant, with traceable, auditable and model-based high quality processes
There are compelling enterprise circumstances for digital transformation and high quality administration on this quickly rising and evolving business. Siemens Accelerated Battery Improvement and Sensible Manufacturing options with closed-loop high quality administration speed up the adoption of clever, environment friendly, and adaptable battery improvement and manufacturing processes. This digital know-how permits improvement facilities and factories to fabricate battery cells, modules, and packs that meet high quality, throughput, price, and sustainability objectives. The insights acquired from each design and operational information enable for steady enchancment and elevated agility. These capabilities empower battery producers to safe a dominant place on this increasing business.
Siemens closed-loop high quality administration options transcend the normal paradigm of the corporate itself, reaching out to the prolonged enterprise. The options strengthen upstream provider collaboration and downstream evaluation and monitoring of core high quality processes. These shut ties with suppliers and auditors are important, particularly because the battery business incorporates steadily up to date high quality requirements and innovates cell chemistries and codecs, new supplies and next-generation sustainable applied sciences.
Study extra about Siemens Battery Sensible Manufacturing options.
[ad_2]